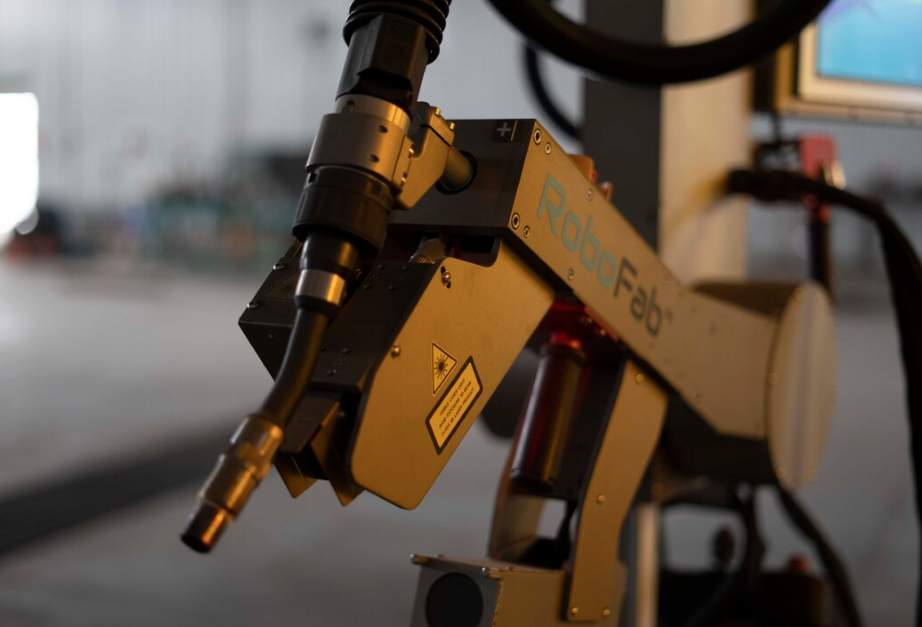
Investing in tube welding equipment is a significant decision for any manufacturing business. The potential benefits, including increased productivity, improved quality, and cost savings, are substantial. However, to justify the investment, it’s crucial to understand the return on investment (ROI) and factors influencing it.
Understanding ROI in Tube Welding Equipment
ROI is the ratio of net profit to the cost of investment. In the context of tube welding equipment, it involves calculating the total savings and revenue generated by the equipment compared to its purchase, installation, and operational costs. For Tube Welding buyers understanding ROI is crucial to making informed purchasing decisions.
Factors Affecting ROI
Several key factors determine the ROI of tube welding equipment:
- Type of Equipment: The specific type of tube welding equipment (TIG, MIG, laser, etc.) will influence its cost, capabilities, and suitability for your production needs.
- Production Volume: Higher production volumes generally lead to a quicker ROI due to increased utilization of the equipment.
- Labor Costs: Automating welding processes can significantly reduce labor costs, contributing to a higher ROI.
- Material Costs: Tube welding equipment can often reduce material waste, leading to cost savings.
- Product Complexity: The complexity of the tube welding process affects the equipment’s utilization and, consequently, the ROI.
- Equipment Maintenance: Regular maintenance is essential to ensure equipment longevity and optimal performance.
- Operator Training: Skilled operators maximize equipment efficiency and minimize downtime.
Calculating ROI
To calculate ROI, you need to determine the following:
- Initial Investment: The cost of purchasing, installing, and setting up the equipment.
- Operational Costs: Ongoing expenses such as electricity, maintenance, and labor.
- Increased Revenue: Additional revenue generated due to increased production or improved product quality.
- Cost Savings: Reductions in labor, material, and energy costs.
Once you have gathered this information, you can calculate the ROI using the following formula:
ROI = (Net Profit / Total Investment) x 100
Improving ROI
To maximize the ROI of your tube welding equipment, consider the following strategies:
- Optimize Equipment Utilization: Ensure the equipment is used efficiently by scheduling production effectively and minimizing idle time.
- Invest in Operator Training: Well-trained operators can increase productivity and reduce errors.
- Implement Quality Control Measures: Consistent product quality reduces rework and scrap, improving overall efficiency.
- Regular Maintenance: Preventive maintenance extends equipment life and minimizes downtime.
- Explore Automation: Integrating automation with tube welding can further enhance productivity and reduce labor costs.
- Consider Equipment Upgrades: Investing in upgrades or additional equipment can improve capabilities and expand production possibilities.
Challenges and Considerations
While tube welding equipment offers significant potential for ROI, challenges may arise. These include:
- Initial Investment: The upfront cost of equipment can be substantial.
- Equipment Complexity: Some advanced equipment may require specialized training and maintenance.
- Integration Challenges: Integrating new equipment into existing production processes can be complex.
- Economic Factors: Market fluctuations and economic downturns can impact ROI.
Conclusion
The ROI of tube welding equipment is a complex calculation influenced by various factors. By carefully considering these factors, conducting a thorough cost-benefit analysis, and implementing strategies to optimize equipment utilization, businesses can maximize their return on investment. It’s essential to view tube welding equipment as a long-term investment that contributes to overall manufacturing efficiency and competitiveness.