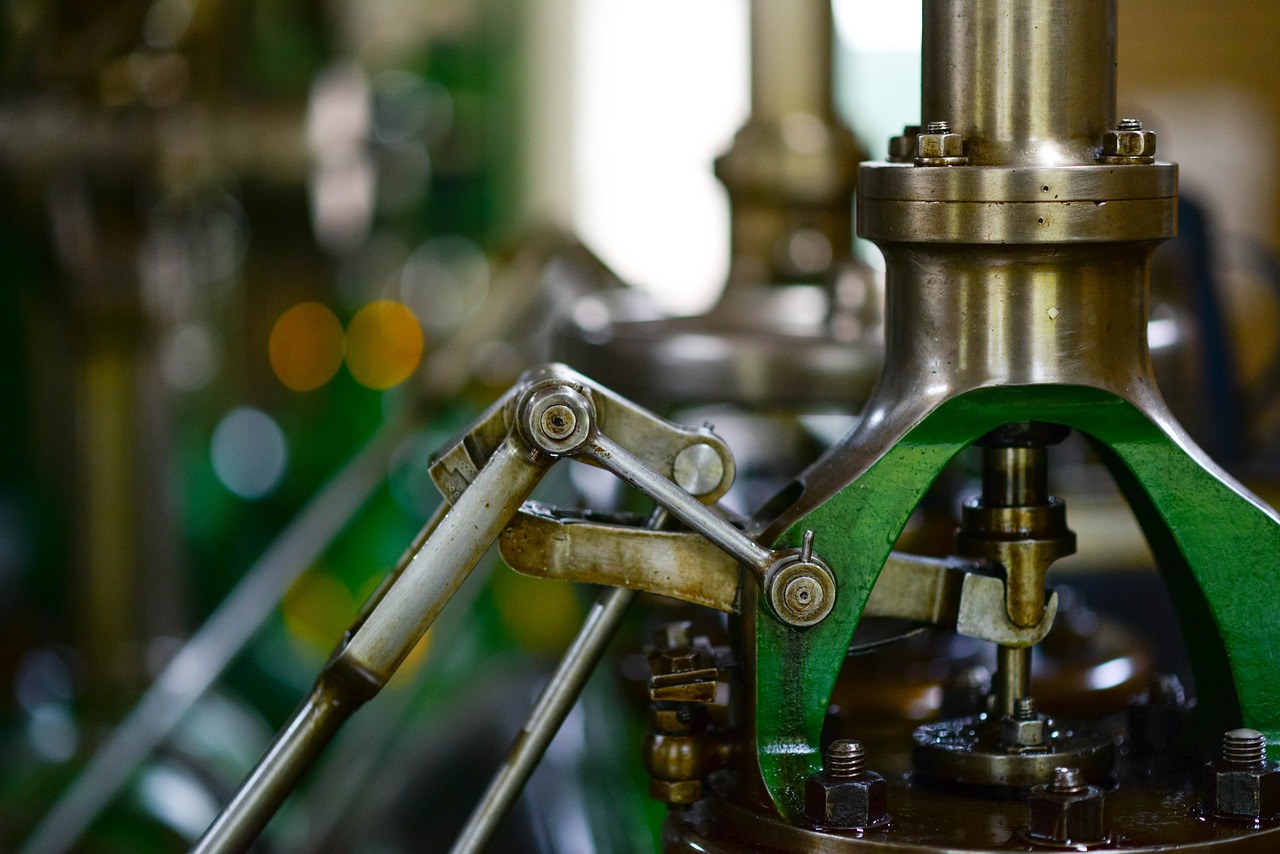
The automotive repair industry is continually evolving, driven by advancements in technology, safety standards, and operational efficiency. For many older automotive workshops, keeping pace with these changes requires strategic upgrades to equipment and infrastructure. Retrofitting older facilities with modern in-ground lifts represents a significant opportunity to enhance functionality, improve safety, and optimize operational efficiency. This article explores the process of retrofitting automotive workshops with in ground lifts, highlighting the benefits and considerations involved in this transformational upgrade.
Understanding In-Ground Lifts: Technology and Benefits
In-ground lifts have become increasingly popular in automotive workshops due to their space-saving design, enhanced safety features, and ergonomic advantages. Unlike traditional surface-mounted lifts, in-ground lifts are installed beneath the workshop floor, providing a flush surface when not in use and rising to lift vehicles for maintenance and repair tasks. Key benefits of in-ground lifts include:
-
Space Optimization: By integrating into the workshop floor, in-ground lifts maximize usable space, allowing for more efficient workflow and increased capacity for servicing multiple vehicles simultaneously.
-
Improved Accessibility: In-ground lifts offer unobstructed access to the vehicle underside, facilitating easier and safer maintenance tasks compared to surface-mounted alternatives. This accessibility enhances technician productivity and reduces the risk of workplace injuries.
-
Durability and Longevity: Modern in-ground lifts are built to withstand heavy usage and harsh operating conditions, offering a longer service life and requiring less frequent maintenance compared to older lifting equipment.
The Need for Retrofitting Older Workshops
Many automotive workshops still rely on outdated lifting equipment, such as surface-mounted lifts or manual jacks, which may limit operational efficiency and pose safety risks. Retrofitting these facilities with modern in-ground lifts addresses several key challenges and aligns with industry trends towards enhanced safety standards, technological integration, and workflow optimization.
1. Safety and Compliance: Older lifting equipment may not meet current safety standards and regulatory requirements, increasing the risk of workplace accidents and liability issues. Retrofitting with modern in-ground lifts ensures compliance with safety regulations, protecting both technicians and workshop owners from potential legal consequences.
2. Technological Integration: Modern in-ground lifts are often equipped with advanced features such as automatic safety locks, digital control systems, and ergonomic designs that enhance operational efficiency and reduce human error. Integrating these technological advancements into older workshops improves overall service quality and customer satisfaction.
3. Workflow Optimization: Outdated lifting equipment may hinder workflow efficiency, leading to longer service times and reduced customer throughput. In-ground lifts facilitate quicker vehicle positioning and easier access to components, enabling technicians to perform maintenance tasks more efficiently and effectively.
4. Space Utilization: Retrofitting with in-ground lifts allows workshops to optimize floor space by eliminating the need for bulky surface-mounted lift structures. This additional space can be repurposed for additional service bays, equipment storage, or customer waiting areas, enhancing overall facility functionality.
Process of Retrofitting with In-Ground Lifts
Retrofitting an older automotive workshop with modern in-ground lifts involves several sequential steps to ensure a successful and efficient upgrade process:
1. Initial Assessment and Planning:
-
Conduct a thorough assessment of the workshop layout, existing infrastructure, and operational needs.
-
Identify suitable locations for installing in-ground lifts based on vehicle traffic patterns, service bay configurations, and space constraints.
-
Develop a detailed retrofitting plan that includes budget estimates, timeline projections, and compliance with local building codes and safety regulations.
2. Infrastructure Preparation:
-
Prepare the workshop floor for in-ground lift installation, which typically involves excavation to accommodate lift pits and ensure proper drainage.
-
Coordinate with utility providers to relocate underground utilities if necessary, ensuring uninterrupted workshop operations during construction.
3. In-Ground Lift Installation:
-
Install in-ground lift components, including hydraulic systems, safety locks, and control panels, according to manufacturer specifications and engineering standards.
-
Conduct rigorous testing and calibration of each lift to verify operational functionality and safety compliance before integrating into daily service operations.
4. Training and Certification:
-
Provide comprehensive training for technicians on the safe operation, maintenance procedures, and troubleshooting techniques for new in-ground lifts.
-
Obtain necessary certifications and documentation to demonstrate compliance with industry standards and regulatory requirements.
5. Integration and Testing:
-
Integrate in-ground lifts into existing workshop management systems, including digital diagnostics, inventory management, and customer service platforms.
-
Conduct operational testing and quality assurance checks to ensure seamless integration with workflow processes and optimal performance.
Benefits of Retrofitting with Modern In-Ground Lifts
Retrofitting older automotive workshops with modern in-ground lifts offers numerous benefits that significantly enhance operational efficiency, safety, and customer satisfaction:
1. Enhanced Safety Standards: Modern in-ground lifts are equipped with advanced safety features, such as automatic locking mechanisms and overload protection systems, minimizing the risk of workplace accidents and ensuring compliance with industry safety standards.
2. Improved Technician Productivity: In-ground lifts facilitate faster vehicle positioning and easier access to components, allowing technicians to perform maintenance tasks more efficiently. This efficiency gains translate into reduced service times and increased service bay turnover rates.
3. Space Optimization: By eliminating the need for surface-mounted lift structures, in-ground lifts optimize floor space within the workshop. This additional space can be utilized for additional service bays, specialized equipment installations, or customer amenities, enhancing overall facility functionality and revenue-generating potential.
4. Long-Term Cost Savings: While the initial investment in retrofitting with in-ground lifts may be higher than maintaining older equipment, the long-term cost savings are significant. Reduced maintenance requirements, improved energy efficiency, and enhanced workflow efficiency contribute to lower operational costs and increased profitability over time.
5. Technological Integration: Modern in-ground lifts can be integrated with digital diagnostic tools, inventory management systems, and customer service platforms, streamlining service operations and enhancing service quality. This technological integration improves overall service delivery and customer satisfaction, positioning the workshop as a leader in automotive repair and maintenance services.
Conclusion
Retrofitting older automotive workshops with modern in-ground lifts is a strategic investment that enhances functionality, improves safety, and optimizes operational efficiency. By addressing the challenges associated with outdated lifting equipment and aligning with industry trends towards technological integration and safety compliance, workshops can elevate their service capabilities and maintain a competitive edge in the evolving automotive repair industry. With careful planning, thorough implementation, and ongoing maintenance, the transition to modern in-ground lifts offers workshops a pathway to sustainable growth, customer loyalty, and operational excellence in automotive service provision.
Incorporating modern technologies such as mini dock leveler further enhances efficiency and operational capabilities, ensuring that automotive workshops remain at the forefront of service excellence and customer satisfaction.